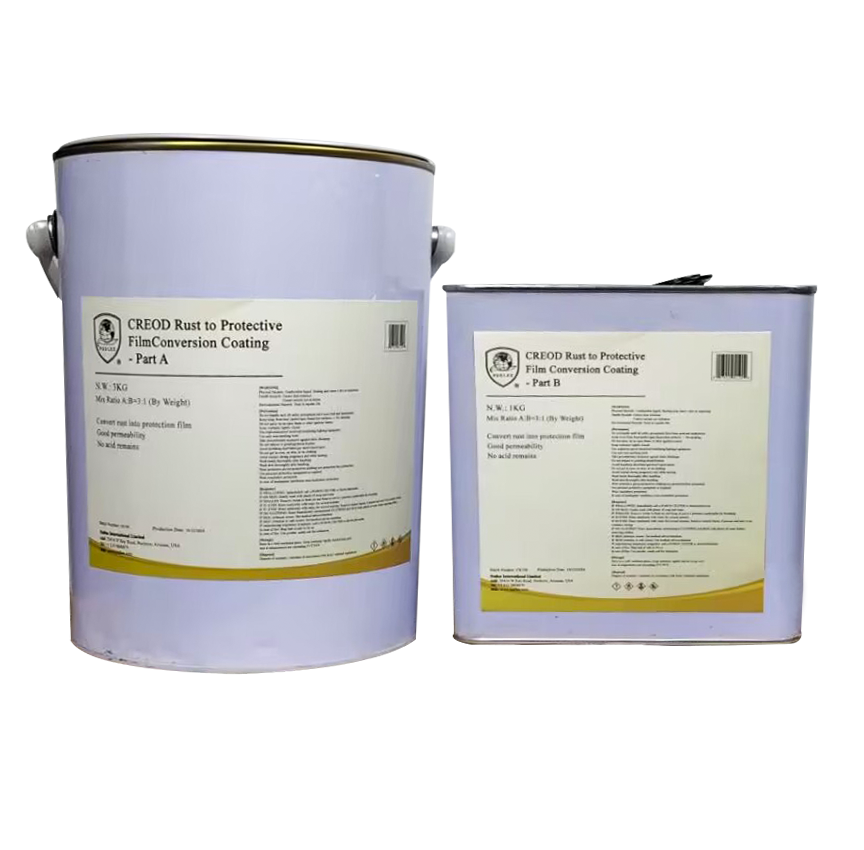
CREOD Coating
CREOD is a revolutionary anti-corrosion coating launched by PodLee (USA) in 2017, developed over 2.5 years. It integrates rust removal and corrosion protection, eliminating the need for traditional acid pickling processes.
CREOD utilizes specially designed alcohol-aluminum-based active molecules that react with rust, converting it into a dense epoxy-metal composite protective film on the substrate surface. This achieves simultaneous rust removal and corrosion protection.
Compared to traditional processes (acid pickling → residue cleaning → coating), CREOD offers significant advantages including rust-tolerant application, high permeability, complete rust removal, no acidic residue, superior corrosion resistance, excellent adhesion, compatibility with topcoats. CREOD is an ideal replacement for conventional methods.
Intended Uses
Rusty metal parts in high-humidity, high-salt environments (e.g., ship hulls, decks, offshore platforms).
Equipment, pipelines, and structures in petrochemical, power, and metallurgical industries.
Large steel structures such as bridges, steel frames, and towers.
Advantages
Rust-tolerant application – Reduces construction costs and safety risks.
High permeability – Suitable for complex structures.
Acid-free residue – Compatible with various topcoats.
Typical Characteristics
Name | Test Data | Testing Standard | |
---|---|---|---|
Cured Density (g/cc) | 1.04 | – | |
Solid Content (%) | 73 – 77 | ASTM D3960 | |
Pencil Hardness (H) | 2 | ASTM D3363 | |
Water Resistance (1000h) | Pass | ASTM D2247 | |
Adhesion (psi/MPa) | Rusted Steel | 435 (3) | ASTM D4541 |
Chemical Resistance (90 Days) |
HCl (10%) | Pass | ASTM G20 |
NaOH (10%) | Pass | ||
NaCl (10%) | Pass | ||
Salt Spray Test (h) | 1000 | ASTM B117 | |
Service Temperature (℉/℃) | -22 (-30) – 194 (90) | – |
Package
4 KG/Kit.
Surface Preparation
Proper surface preparation is critical for optimal performance:
Degrease and desalinate surfaces. Rinse salt residues with freshwater in marine environments.
Remove contaminants and manually derust using wire brushes or sandpaper (SA1 grade).
Wipe surfaces clean with a dry cloth to remove moisture and loose rust.
Mixing
Ensure ambient temperature is 50 – 104℉ (10 – 40°C).
Mixing ratio: 3:1 (By Weight).
Weigh components accurately and stir mechanically for 3 – 5 minutes.
Application
Apply using a brush or roller.
Single-coat thickness: 40 μm.
Allow ≥ 18 hours between coats.
Works with epoxy, polyurethane, and fluorocarbon topcoats.
Coverage
Based on a 40 μm thickness: 1 kg kit will cover 15 m 2 (161 ft 2).
Pot Life After Mixing
50℉ (10℃) – 6 h 70℉ (25℃) – 4 h 104℉ (40℃) – 2 h
Curing Schedule
Temperature | 50℉ (10℃) | 70℉ (25℃) | 104℉ (40℃) |
---|---|---|---|
Surface Dry (h) | 24 | 18 | 12 |
Complete Curing (h) | 72 | 48 | 36 |
Clean Up
Clean tools immediately after use with solvents (acetone, xylene, alcohol, etc.).
Storage
Store between 10°C (50°F) and 32°C (90°F).
Unopened product shelf life: 1 year.
Safety
Before using any products, review the appropriate Material Safety Data Sheet (MSDS) or Safety Sheet for your area. Follow standard confined space entry and work procedures, if appropriate.