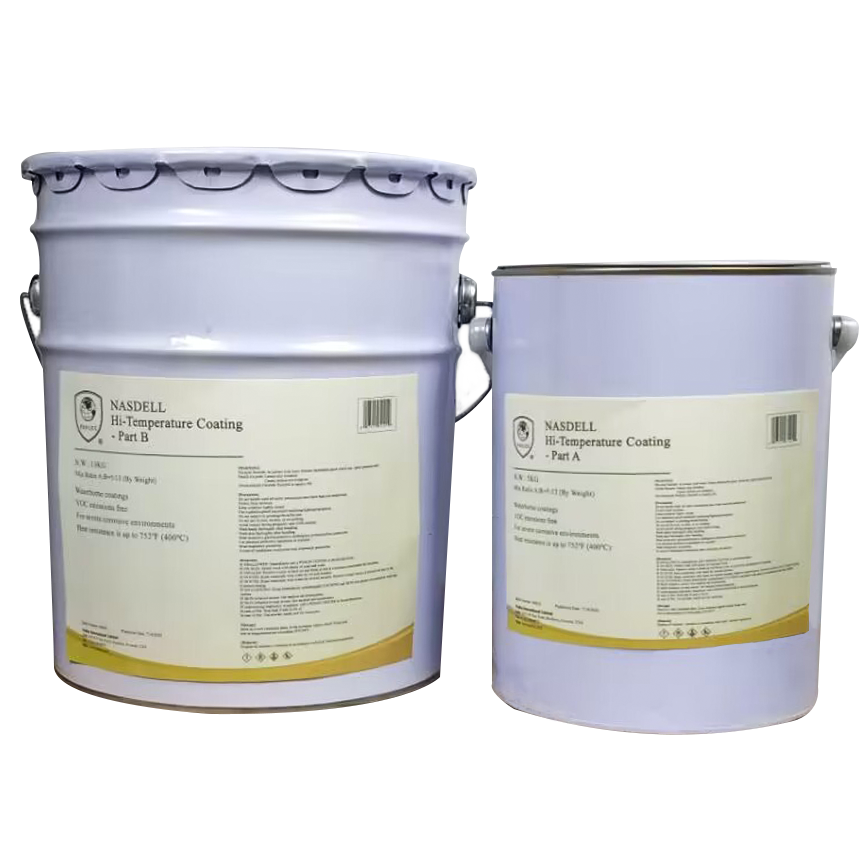
NASDELL Coating
Traditional water-based inorganic zinc-rich coatings use water-based inorganic silicate emulsions as binders and high-purity zinc powder as filler. Their anti-corrosion mechanism combines cathodic electrochemical protection and physical barrier protection. However, due to the polycondensation reaction of silicate materials during curing, unrelieved shrinkage stress is generated, leading to surface cracking under thermal cycling conditions.
NASDELL High-Temperature Coating, developed through our proprietary fluorine-modified silicone resin composite technology, restructures the molecular architecture of traditional silicate systems. This innovation enhances coating flexibility, temperature resistance, and weather resistance, raising the maximum service temperature to 752℉ (400°C). It overcomes the cracking issues of conventional inorganic zinc-rich coatings under harsh thermal cycling conditions.
Intended Uses
Can be used as a primer in combination with epoxy primers and high-performance topcoats to provide long-term heavy-duty corrosion protection. Typical applications include: bridges, offshore platforms, hull surfaces above the waterline, superstructures and decks of ships, non-immersed steel structures and pipeline exteriors.
Can also be applied as a single coating to protect high-temperature components such as steam pipelines and heat exchangers.
Advantages
Outstanding environmental performance: VOC emissions as low as 7 g/L – far below the 50 g/L limits set by the U.S. and EU.
Excellent cathodic protection and salt spray resistance – significantly improves anti-corrosion reliability and safety.
Superior high-temperature performance – operates long-term at 752℉ (400°C).
Resistant to immersion in solvents and oils – broad application scope.
Typical Characteristics
Name | Test Data | Testing Standard | |
---|---|---|---|
Cured Density (g/cc) | 2.65 | – | |
Solid Content (%) | 65 | ASTM D3960 | |
Pencil Hardness (H) | 2 | ASTM D3363 | |
Water Resistance (1000h) | Pass | ASTM D2247 | |
VOC Emissions (g/L) | 7 | ASTM D3960 | |
Adhesion (psi/MPa) |
Sandblasted steel | 725 (5) | ASTM D4541 |
Chemical Resistance (90 Days) |
HCl (10%) | Pass | ASTM G20 |
NaOH (10%) | Pass | ||
NaCl (10%) | Pass | ||
Salt Spray Test | 10000 | ASTM B117 | |
Service Temperature (℉/℃) | -22 (-30) – 752 (400) | – |
Package
18 KG/Kit.
Surface Preparation
Proper surface preparation is critical for optimal performance:
Remove oil and salt from the surface. For marine environments, rinse thoroughly with fresh water to eliminate salt residues.
Remove contaminants and perform mechanical derusting or manual grinding (derusting grade SA2.5 or ST3).
Wipe the surface with a clean cloth to remove residual moisture, dust, or loose rust.
Mixing
Ensure ambient temperature is 50 – 104℉ (10 – 40°C).
Mixing ratio: 5:13 (By Weight).
Weigh components accurately and stir mechanically for 3 – 5 minutes.
Application
Apply using a brush or roller.
Single-coat thickness: 60 μm.
Minimum recoating interval: 6 hours.
Coverage
Based on a 60 μm thickness: 1 kg kit will cover 4.3 m 2 (46 ft 2).
Pot Life After Mixing
50℉ (10℃) – 3 h 70℉ (25℃) – 2 h 104℉ (40℃) – 1.5 h
Curing Schedule
Temperature | 50℉ (10℃) | 70℉ (25℃) | 104℉ (40℃) |
---|---|---|---|
Surface Dry (min) | 25 | 15 | 10 |
Complete Curing (h) | 10 | 6 | 4 |
Clean Up
Clean tools immediately after use with solvents (acetone, xylene, alcohol, etc.).
Storage
Store between 10°C (50°F) and 32°C (90°F).
Unopened product shelf life: 1 year.
Safety
Before using any products, review the appropriate Material Safety Data Sheet (MSDS) or Safety Sheet for your area. Follow standard confined space entry and work procedures, if appropriate.