Safety
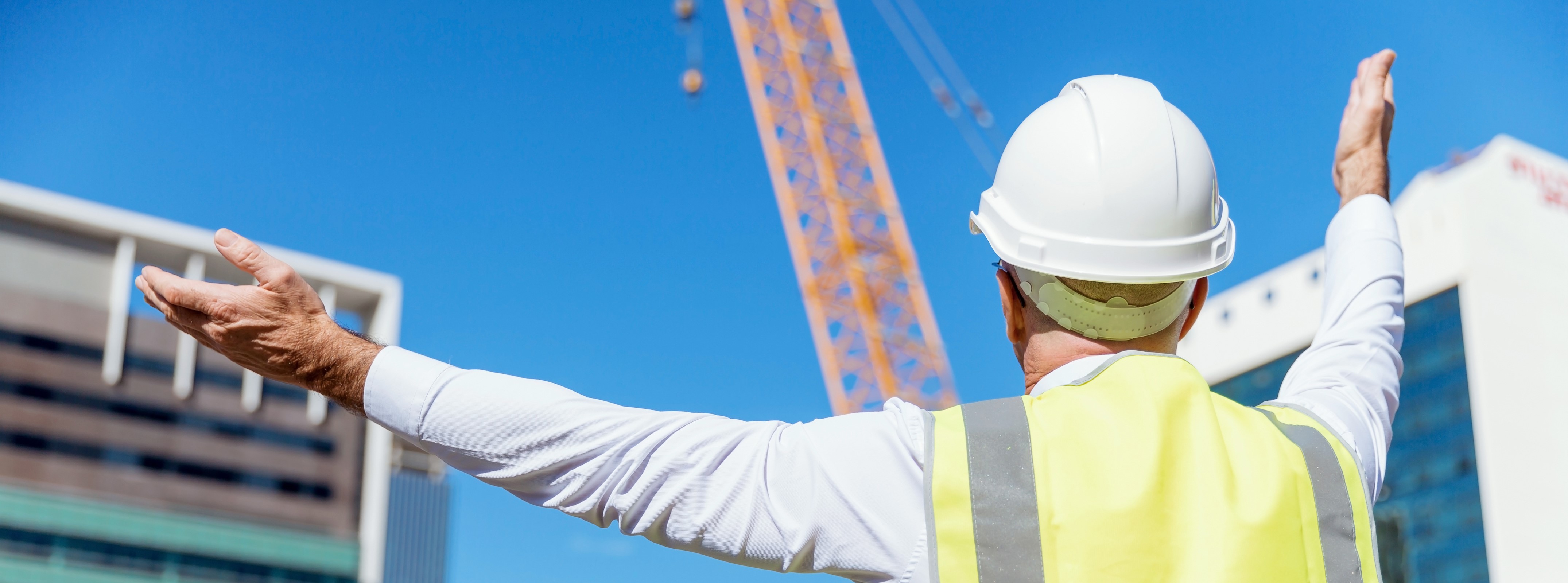
At Podlee, safety is the cornerstone of our operations. We believe that every individual —from our employees and contractors to our customers and neighbors — deserves to work and live in an environment free from preventable harm. Our Safety Policy reflects our unwavering commitment to fostering a culture of vigilance, responsibility, and continuous improvement. It is built on four core principles: Prevention, Preparedness, Accountability, and Innovation.
1. Cultivating a Safety-First Culture
We prioritize safety as a shared value, not just a compliance requirement.
- Leadership Commitment: Managers and supervisors lead by example, ensuring safety protocols are integrated into daily workflows and decision-making.
- Employee Engagement: Empower employees to actively identify hazards, report near-misses, and participate in safety committees.
- Training Excellence: Mandatory, role-specific training programs cover equipment operation, chemical handling, emergency procedures, and OSHA standards.
- Behavior-Based Safety: Regular safety audits, toolbox talks, and recognition programs reinforce safe behaviors and accountability at all levels.
2. Operational Safety & Risk Management
We mitigate risks through rigorous systems and cutting-edge practices.
- Hazard Analysis: Conduct thorough risk assessments for all processes, from raw material handling to product distribution.
- Engineering Controls: Invest in state-of-the-art machinery, automated systems, and fail-safe mechanisms to minimize human error.
- PPE & Ergonomics: Provide industry-leading personal protective equipment (PPE) and design workspaces to reduce physical strain and injury risks.
- Process Safety Management (PSM): Implement strict protocols for managing highly hazardous materials, including regular inspections, maintenance, and lockout/tagout procedures.
3. Product Safety & Supply Chain Accountability
Safety extends to how our products are designed, used, and transported.
- Safe Design Principles: Formulate coatings and lubricants to meet or exceed global safety standards (e.g., REACH, EPA) for storage, handling, and application.
- Supply Chain Collaboration: Partner with suppliers and distributors who adhere to our safety expectations, including proper labeling, packaging, and transportation practices.
- Customer Education: Provide clear instructions, safety data sheets (SDS), and technical support to ensure products are used correctly and responsibly.
4. Emergency Preparedness & Resilience
We plan for the unexpected to protect people and communities.
- Robust Response Plans: Maintain up-to-date emergency action plans for scenarios such as chemical spills, fires, or natural disasters.
- Drills & Training: Conduct regular emergency simulations with employees, local responders, and community stakeholders to ensure readiness.
- Crisis Communication: Establish transparent communication channels to swiftly inform employees, authorities, and the public during incidents.
5. Continuous Improvement & Transparency
Safety is a journey of constant learning and adaptation.
- Data-Driven Insights: Track leading and lagging indicators (e.g., incident rates, near-misses) to identify trends and address root causes.
- Technology Adoption: Leverage IoT sensors, AI-driven analytics, and wearable tech to monitor workplace conditions in real time.
- Stakeholder Collaboration: Work with industry groups, regulators, and NGOs to advance safety standards and share best practices.
- Transparent Reporting: Publish annual safety performance reports and progress toward our goal of zero recordable incidents.