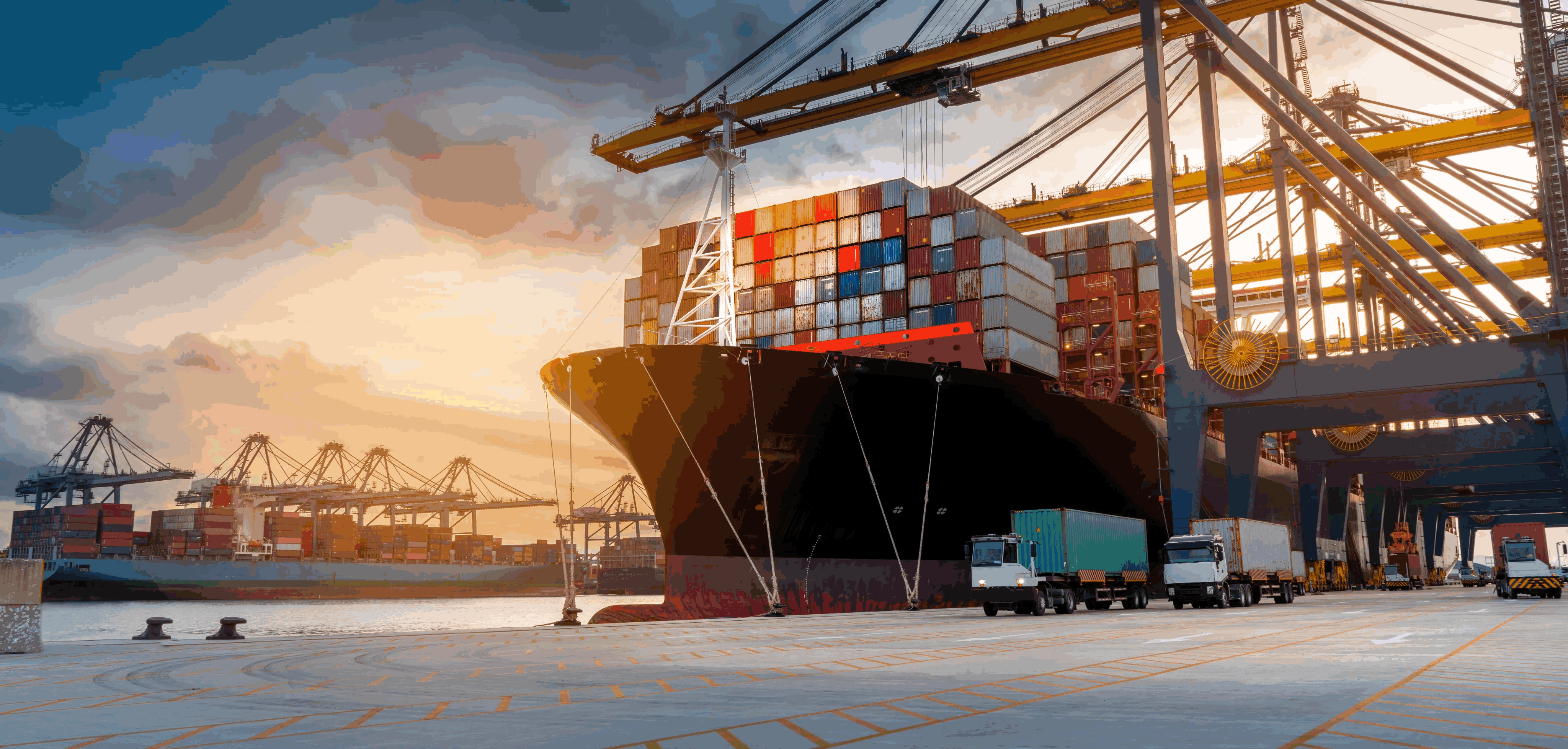
Welcome to PodLee International
Your trusted partner for lubricating and anticorrosion solutions.
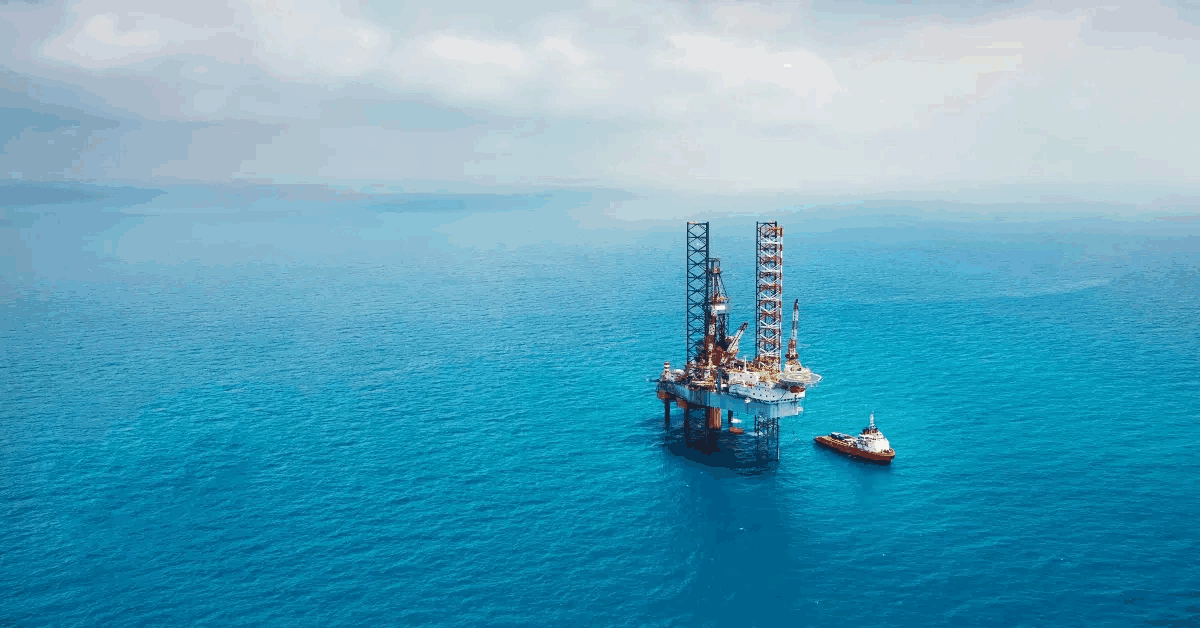
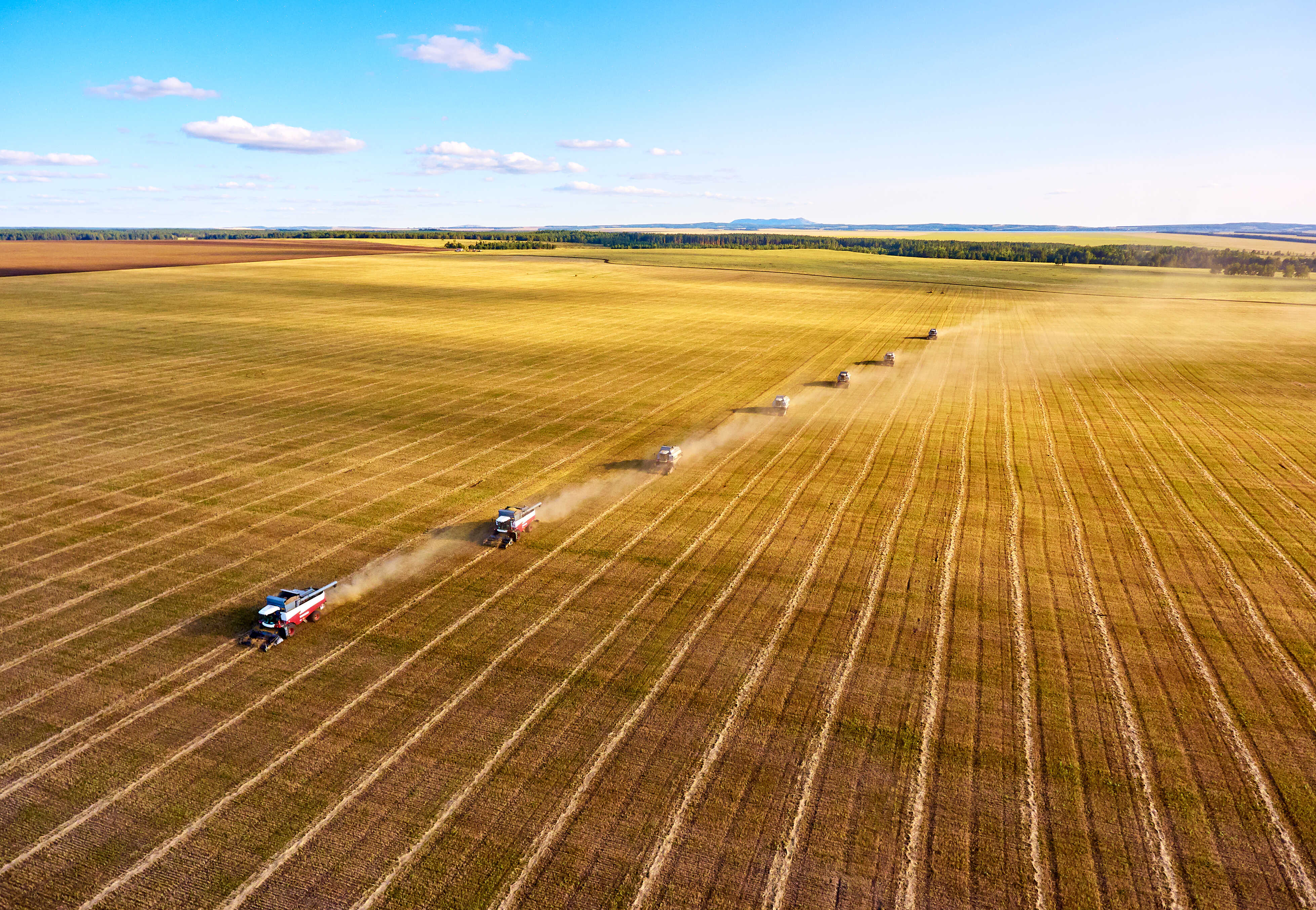
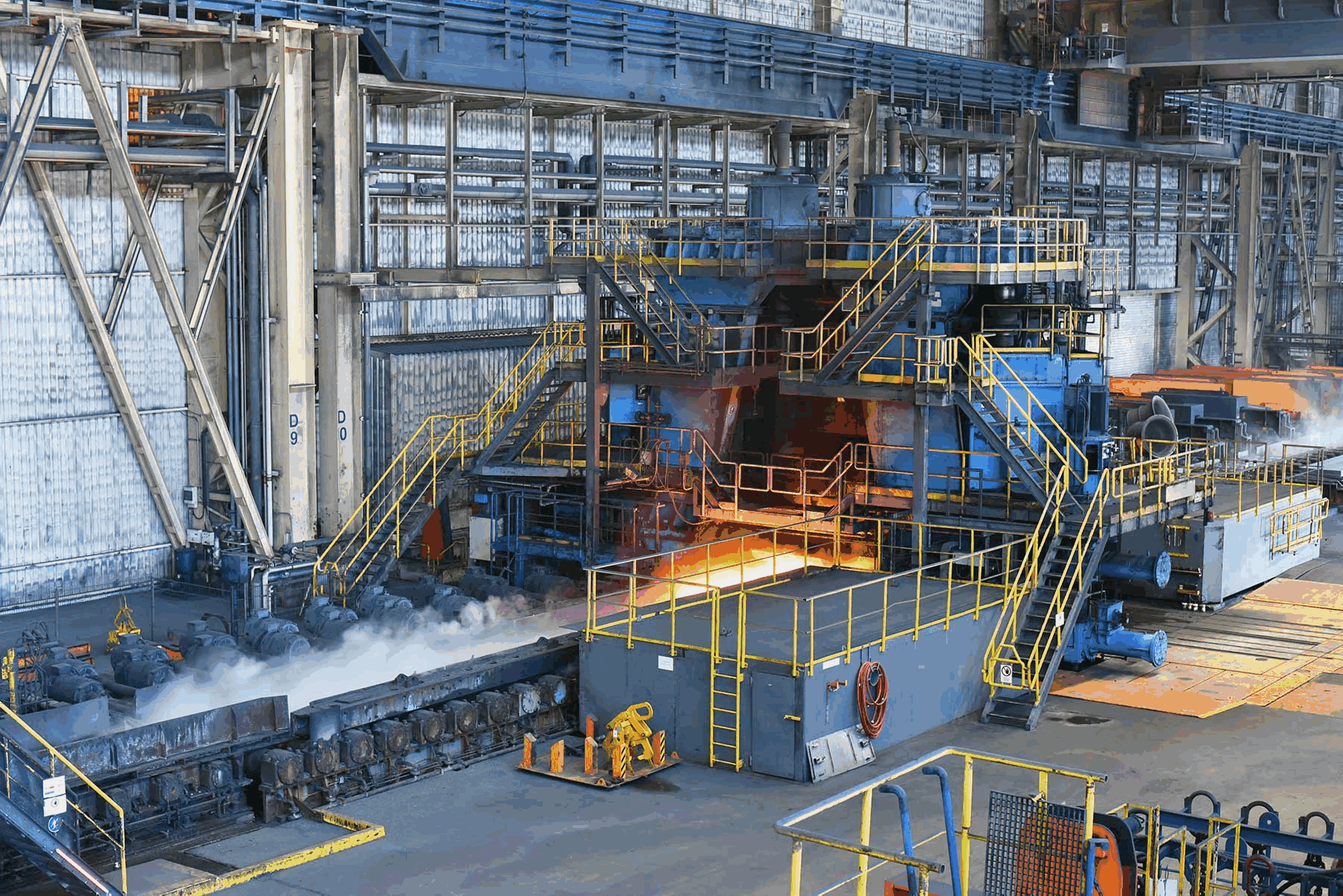
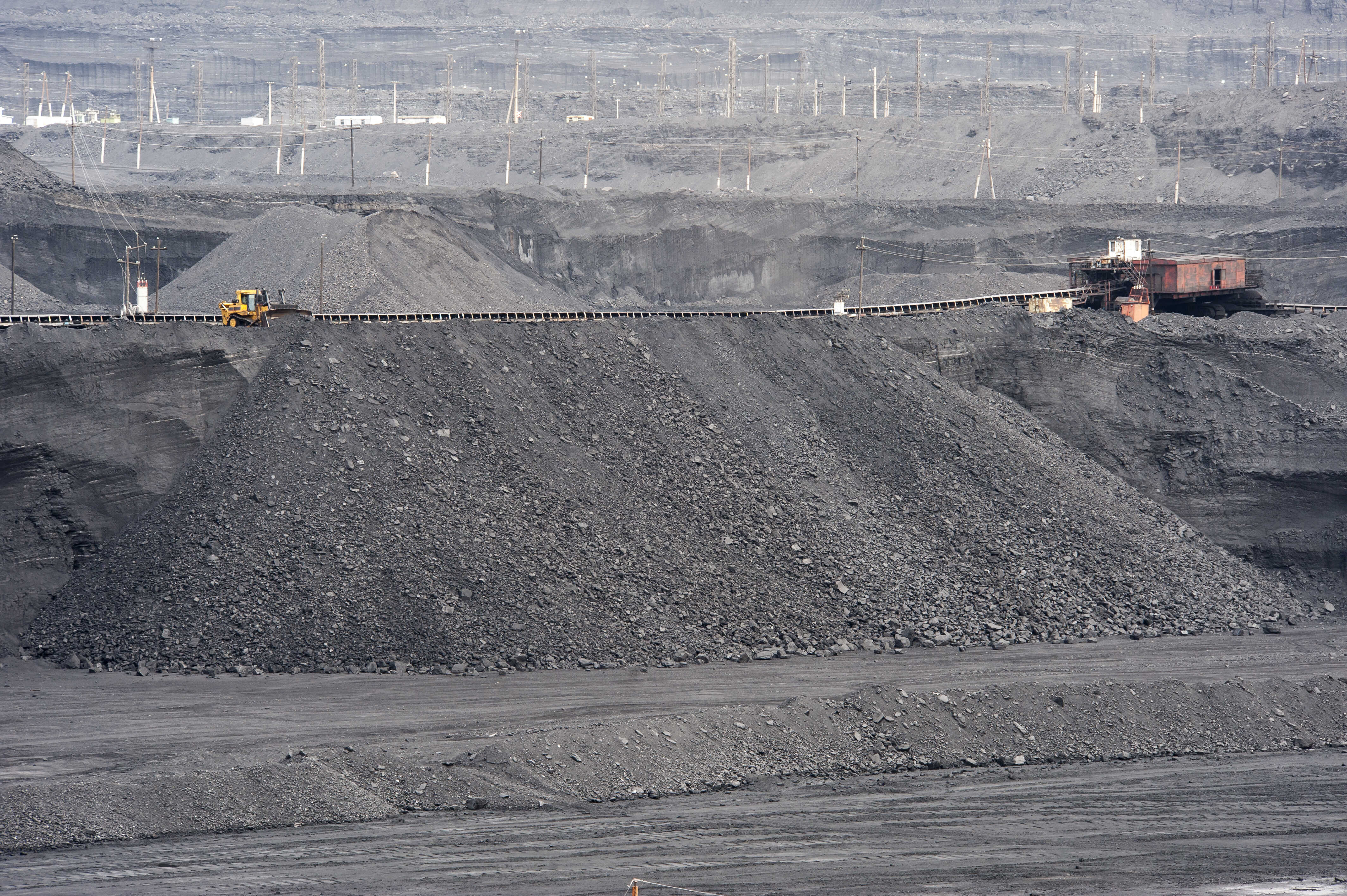
Our USA Factory
Located in Arizona, our USA manufacturing facility is the cornerstone of innovation and precision in producing high-performance anticorrosion coatings and industrial lubricants. Equipped with cutting-edge production technology and automated systems, we ensure unmatched efficiency and consistency across every batch. Our factory operates under a rigorous quality control framework, adhering to international standards and meticulous testing protocols to guarantee products meet the highest demands of durability and reliability.
Led by a team of seasoned professionals and supported by skilled technicians, we combine advanced manufacturing practices with decades of expertise. From raw material sourcing to final delivery, every step is optimized for excellence, ensuring seamless integration with our in-house R&D lab to rapidly implement breakthrough innovations.
Committed to sustainability and operational excellence, our USA facility not only serves as a hub for domestic and global supply but also reflects our unwavering dedication to empowering industries with solutions built to endure the toughest environments.
Our U.S. R&D Lab
At the forefront of innovation, our state-of-the-art R&D lab in the United States serves as a hub for groundbreaking research and technological advancement. Equipped with the most sophisticated and high-precision experimental machinery, including cutting-edge instrumentation for petrochemical engineering, chemical industry, material science, and nanotechnology etc., we empower our teams to push the boundaries of what’s possible.
Our facility brings together a world-class team of engineers, scientists, and researchers —highly skilled professionals with expertise spanning. Their collaborative spirit, combined with a relentless pursuit of excellence, drives transformative solutions that address today’s most complex challenges and anticipate tomorrow’s opportunities.
By merging precision technology with visionary talent, we are committed to delivering innovations that redefine industries, enhance global competitiveness, and shape the future. Partnering with leading academic institutions and industry pioneers, our lab stands as a testament to the power of curiosity, expertise, and cutting-edge infrastructure.
Solution of High-Performance Coatings for Metal Protection
In the demanding environment of marine applications, corrosion and wear pose constant threats to critical infrastructure. One standout example of our advanced coating technology in action is its successful deployment on metal pipe fittings for a VLCC. Over a rigorous three-year service period, our proprietary coating system provided unparalleled protection, maintaining structural integrity and performance until the fittings were systematically dismantled during a scheduled maintenance cycle.
The Challenge
Exposed to saltwater, temperature fluctuations, and abrasive conditions, the customer’s pipe fittings faced accelerated corrosion, risking leaks, downtime, and costly replacements. Traditional coatings had failed to meet the required lifespan, prompting the need for a robust, long-term solution.
Our Solution
Our team engineered a high-performance, multi-layer coating system tailored for marine environments:
- Base Layer: A dual ingredient rust-devouring coating designed to convert rust into protective film and adhere tightly to metal surfaces, resisting saltwater penetration.
- Intermediate Layer: An all-purpose hybrid epoxy - intermetallic compound blend coating for thermal stability and abrasion resistance.
- Top Layer: A nano ludox based hydrophobic coating intended for high temperature exposures in chemically aggressive applications where the risk for thermal cycling may be present. It is highly resistant to a wide range of inorganic as well as organic acids and hydrocarbon based chemical compounds.
Results
- Zero Corrosion: After three years of continuous exposure, the fittings showed no signs of pitting, cracking, or surface degradation.
- Cost Efficiency: Eliminated unplanned maintenance and extended the time between scheduled overhauls by 70%.
- Validation: Post-dismantling inspection confirmed the coating’s integrity, with performance metrics exceeding industry benchmarks for corrosion resistance by 80%.
Why It Matters
This success underscores our commitment to delivering solutions that endure extreme conditions while reducing lifecycle costs. By combining advanced materials science with real-world expertise, we empower industries to operate safely, sustainably, and efficiently — even in the harshest environments.
Solution of High-Performance Lubricants for Machinery Manufacturing Excellence
In the high-stakes world of heavy machinery manufacturing, equipment reliability is the cornerstone of productivity. A global leader in industrial machinery production has partnered with Podlee to overcome persistent challenges in maintaining their mission-critical production lines. By implementing our Heavy Duty Industrial Gear Oil and High Viscosity Index Anti-Wear Hydraulic Oil, the customer achieved unprecedented operational stability, transforming their efficiency, safety, and total cost of ownership.
The Challenge
The manufacturer’s equipment — operating under extreme loads, temperature variations, and 24/7 cycles — faced accelerated wear, unplanned downtime, and rising maintenance costs. Conventional lubricants failed to provide consistent protection, leading to frequent breakdowns that disrupted production timelines and safety protocols.
Our Solution
Our engineering team delivered a tailored lubrication strategy powered by:
- Heavy Duty Industrial Gear Oil: Engineered with advanced extreme-pressure (EP) additives and superior thermal stability to withstand shock loads and prevent micropitting in high-torque gear systems.
- High Viscosity Index Anti-Wear Hydraulic Oil: Formulated to maintain optimal viscosity across temperature swings, minimizing internal friction and component wear in hydraulic pumps, valves, and actuators.
Results
- Stable Operations: Equipment maintained peak performance for over 12,000 hours without degradation, eliminating unplanned stoppages.
- Extended Component Life: Gear and hydraulic system wear reduced by 60%, doubling maintenance intervals.
- Cost Savings: Annual lubrication-related expenses dropped by 35%, driven by lower fluid consumption, reduced waste, and minimized downtime.
- Enhanced Safety: Consistent lubrication performance mitigated overheating risks and leakage incidents, aligning with stringent workplace safety standards.
Why It Matters
This partnership exemplifies how cutting-edge lubrication science can turn operational pain points into competitive advantages. By protecting machinery at the molecular level, our oils not only safeguard productivity but also empower manufacturers to meet sustainability goals through resource efficiency and waste reduction.